Over ten years expertise in conformal cooling
- Reduced cycle time
- Optimised reliability and quality of tools over time
Integrated design expertise
Mould tuning
We design and produce multi-impression moulds (up to 48 cavities) and single- or dual material moulds.
Our in-house Design Office makes DPH proficient in moulds from A to Z, from design to finish, incorporating manufacture and control.
- Feasibility study
- Co-design
- Support from a project leader
- Part and product design
- Integrated mould study
- Mechanical and software skills with CAD resources
Our moulds are suitable for injecting all types of material:
- polymers: ABS, PS, PP, PC, PE, PBT, PMMA, PA6, PA6.6, PPA, PA46, POM, PA11, PA12, PET, PBT, PPA, SEBS-TPE, TPU.
- technical materials: PEEK, PPSU, LCP, PPS, etc.
- rubber vulcanised elastomer: FKM, HNBR, SBR, Nitrile, EPDM, VMQ...
For all types of part:
- Technical parts
- Visible parts
- Plastic and insert overmoulding
- Demolding of complex parts
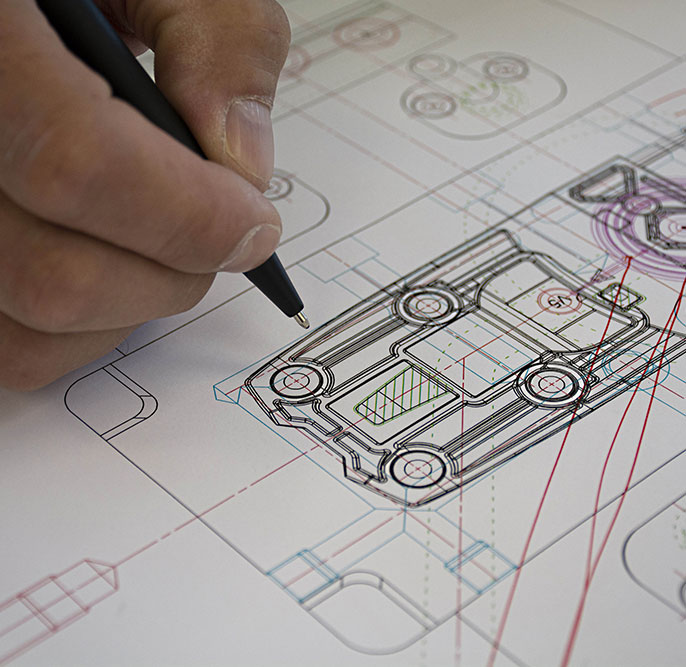

Four steps in your mould project
- Co-design
- Tooling design
- Tooling manufacture and development
- On-site support at start-up
Our resources
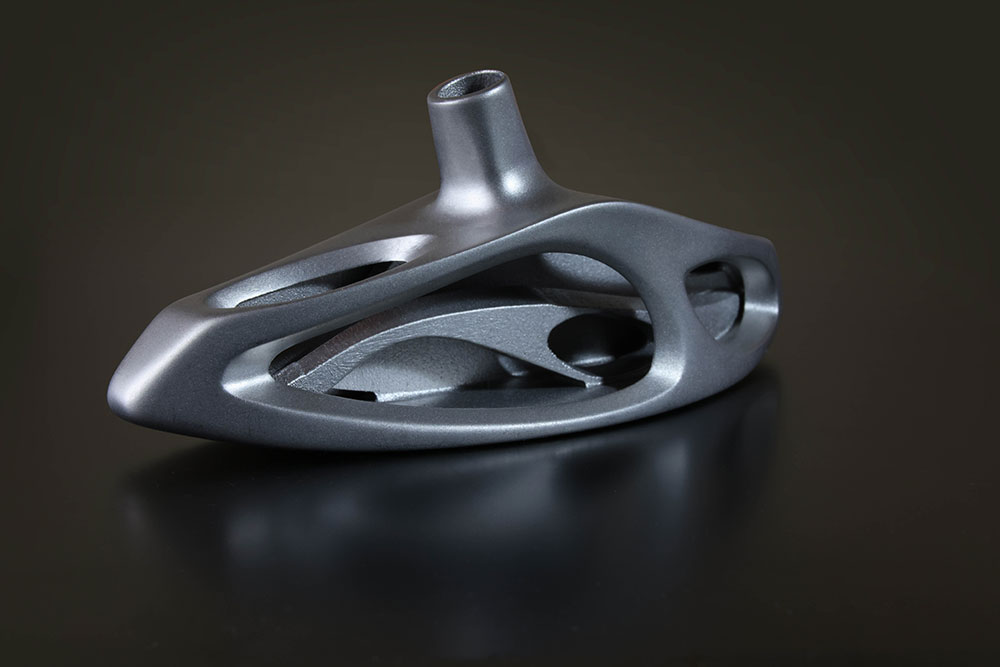
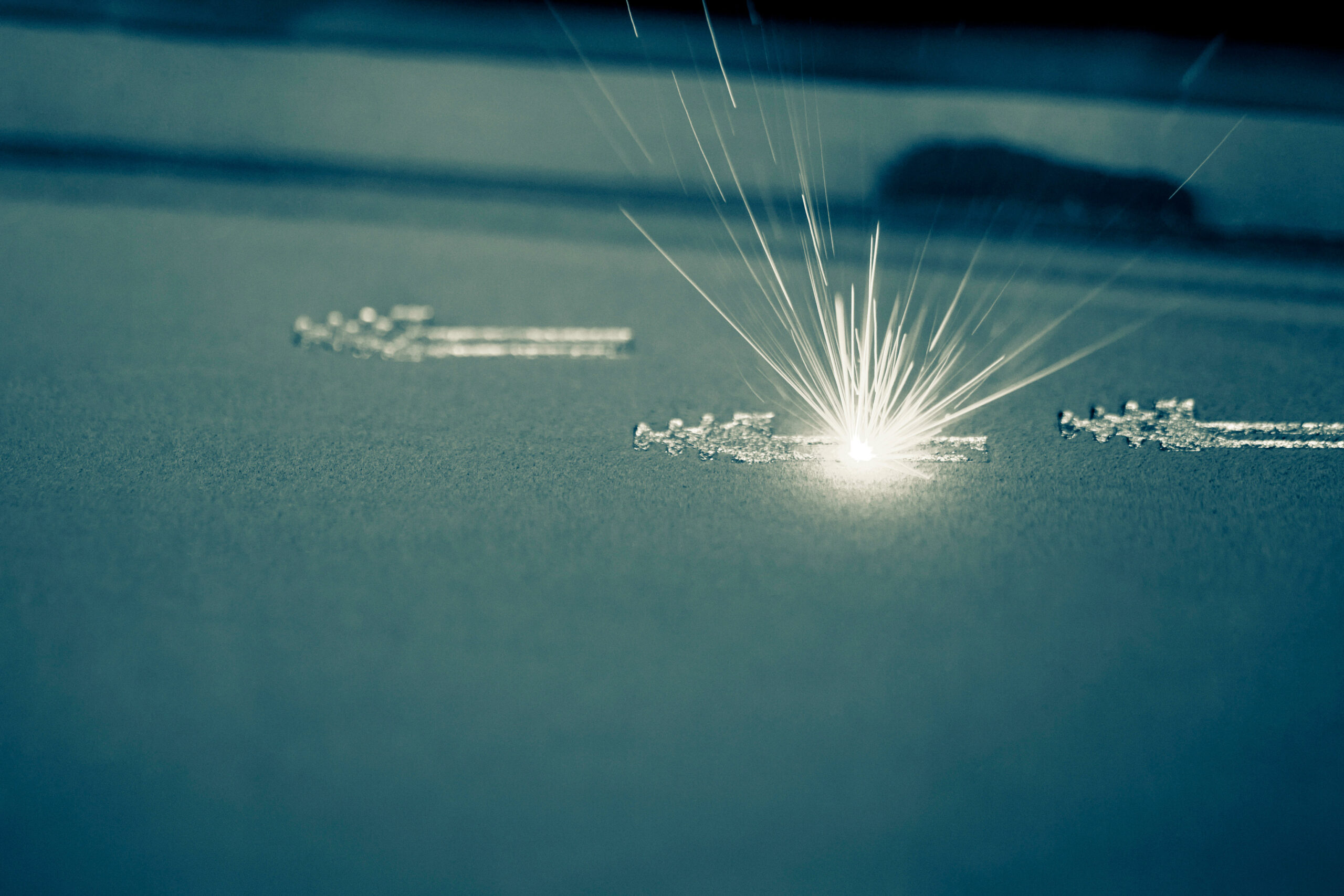
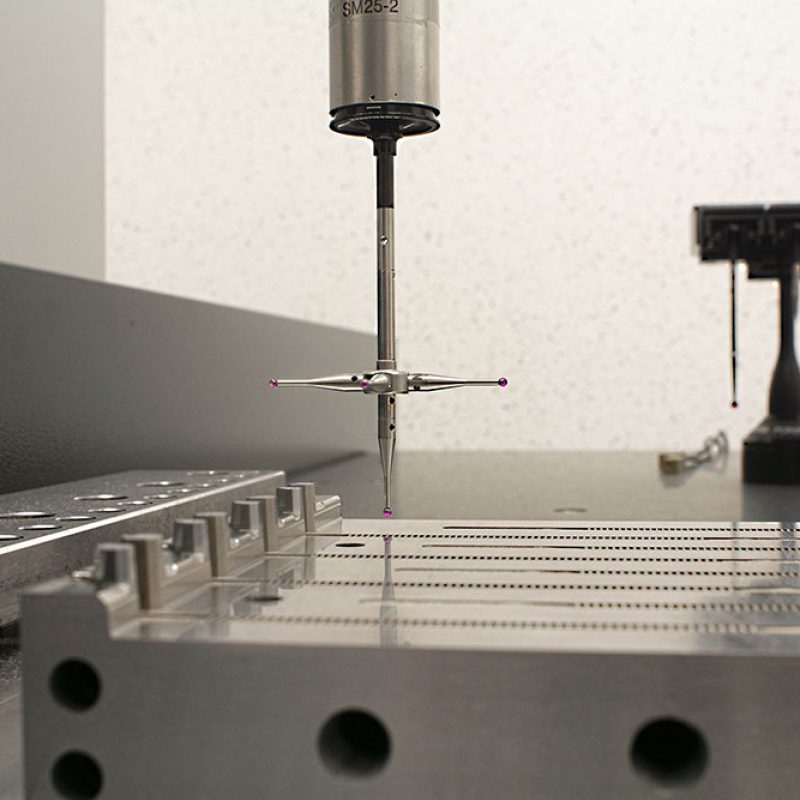
CAD/CAM
Between 3D parts and machining, we programme machining pathways
- We have equipment and design software programs for use in supporting your projects through their entire process.
- Missler CAD/CAD-CAM
MACHINING
Our machining resources are constantly changing.
Two new milling machining were acquired during 2022.
A very high precision, three-axis centre for finishing our cavities and another for our cavities preparations and finishes replaced ageing equipment.
Two new milling machining were acquired during 2022.
A very high precision, three-axis centre for finishing our cavities and another for our cavities preparations and finishes replaced ageing equipment.
Metal 3D printing by laser fusion
We can use our machine to adjust our cavities, which would not have been possible with traditional machinery.
Control and metrology
- Control of integrated parts with CMM, three-dimensional measuring machine, in air-conditioned premises.
- Measuring columns
- Contactless control machine
Mould tuning
Final tuning of our tools is naturally taken into account in our services after tests on our injection machines or in our customers' workshop.
Mould maintenance
With our various handling resources (5 T gantry crane and 2.4 T fork-lift truck), we are able to handling tools up to 4 T without trouble, be they tools manufactured by use or from other sources.
Machinery
We are equipped with
- High-precision machining centre for finishing our impressions
- Robotised, five-axis machining centre to produce our electrodes and machining some of our impressions
- Three-axis machining centre to prepare our impressions or create our structures
- Numerically-controlled lathe which can also be used for hardening machining
- Two erosion machines by part and electrode robotised sinking
- Two wire cutting machines with a wire Ø from 0.1 mm
- Three profile surface grinders
- Traditional drilling and milling machines
- Laser etching machine